Benefits of Prefabricated Modular/Podular BioPharma Facility Construction
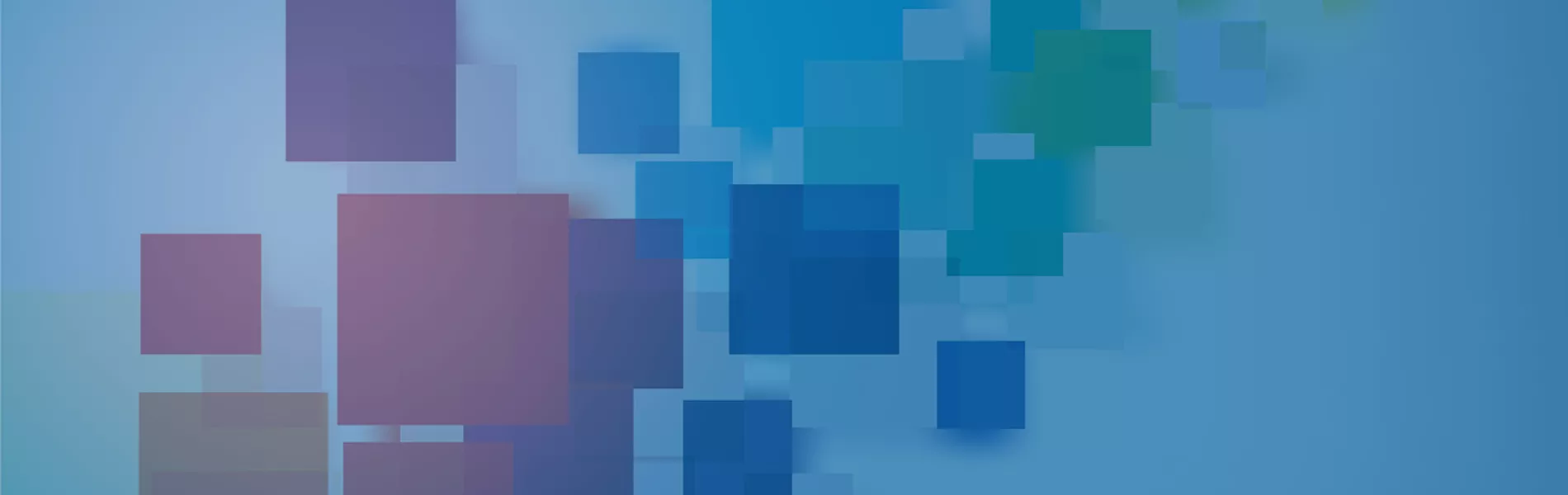
The scientific community is well aware of the impacts of natural disasters. Hurricanes, earthquakes and wildfires have halted manufacturing processes and caused major drug shortages in the U.S. alone. In addition, the World Health Organization (WHO) draws our attention to remote and rural areas of our global community, begging for innovative solutions to deliver vital therapeutics in third-world countries.
As noted by Sarah Mancini, PhD, and Lisa J. Graham, PhD, PE, in the 27 August iSpeak Blog, "...there is opportunity to leverage innovative manufacturing processes….and an agile mindset to adapt to the current needs of patients.”
An emerging trend that has been facilitated by the acceptance of continuous manufacturing and the resultant enablement of small footprint equipment trains is the emergence of prefabricated modular/podular biopharma facilities. These facilities and the design concepts behind them have the potential to address the impacts of natural disasters and fulfill the needs of underserved populations in the global community.
Alternatives to Conventions
Conventional manufacturing facilities require extensive capital outlay and construction time. Although designed to last more than 20 years, these brick-and-mortar facilities contain built-in operating equipment anchored into the facility’s substructure, mandating major renovation for equipment reconfiguration and upgrades.
Modular facilities are also brick-and-mortar construction designed to last more than 20 years, with all major utilities embedded in the building’s infrastructure. However, operating equipment is prefabricated offsite, with skid-mounted platforms subsequently integrated into the facility. The skid-mounted platforms enable reconfiguration and equipment updates without the costs and time constraints of major renovations.
Podular facilities differ substantially from conventional manufacturing plants. Also constructed of brick-and-mortar and designed to last more than 20 years, podular facilities can be assembled in warehouses that contain basic utilities, such as water and electricity, anchored to the infrastructure. Autonomous shells (PODS) and modular, skid-mounted equipment platforms are prefabricated offsite and shipped to the location for onsite assembly. Utilities such as HVAC, process control and hepa filtration systems are pre-integrated into the PODs, enabling inter- and intra- facility reconfiguration of the entire operational factory.
The benefits of modular/podular designs are worth noting:
- Lower onsite project complexity
- Compressed timelines through the application of parallel vs. sequential construction practices
- Reduced financial risk since investment decisions can be made based on current needs, with expansion predicated on evolving capacity demands
- Mitigation of obsolescence through the use of repurposable assets (PODs)
- Additional benefits include:
- Staged launch: Launch production at a fraction of the peak market forecast is possible since scale-out through facility replication or conventional tech transfer to a brick and mortar facility can be invoked as the demand grows
- Be where the patients are: Personalized treatments such as CAR-T together with time sensitive cold chain requirements would benefit from manufacturing operations near the patients. Modular cell therapy units can reduce time to treatment and eliminate the cold chain transportation challenges.
- Technology transfer: Mitigate risk by replacing the time, expense and variability of traditional tech transfers and upgrades through facility replication or transfer of the entire unit to another location (see Transportability below)
Evolving Paradigm: Factory Transportability
Combining modular with podular designs leads to yet another positive consequence: factory transportability.
Factory transportability promises many unique applications for the global community. For example, bench-top size drug production units could be transported on the back of a truck or the back of a person. Such mini-factories would facilitate drug delivery to third-world countries with limited infrastructures.
Continuous manufacturing processes have allowed for much smaller equipment delivering a consistent high-quality product stream using a smaller facility footprint and allowing for some products greater use of certain single use components.
Miniaturized modular/podular facilities further enable drug-production capabilities on a global scale. Lonza and Pfizer, for example, separately collaborated with GE Healthcare’s KUBio to build facilities based on single-use bioprocessing technologies integrated into a prefabricated shell. These “factories in a box” are stacked onsite to create a >15,000 m2 multi-purpose site.
Pfizer also collaborated with G-CON Manufacturing and GEA to install a prefabricated autonomous oral solid dose manufacturing facility in an existing Pfizer warehouse. The facility was designed to enable disassembly and relocation to another site. The continuous manufacturing unit has been approved by the FDA to manufacture commercial supplies of DaurismoTM (glasdegib), with additional projects expect to follow in the future. View the innovative facility in this short video.
Merck partnered with G-CON to build the Formulation Laboratory Experimental Center (FLEx), a multi-modality, podular development with production spaces that can be moved within or outside FLEx. The design also allows easy reconfiguriguration for transport to another location without requiring capital expense for renovations.
Innovation, coupled with recognition of natural events and underserved populations, furthers the advancement of healthcare equality across the globe. As a community of scientists, we welcome the opportunity to serve the global population regardless of location and natural disasters.
You can learn about additional solutions during the Innovative Forum Track sessions at 2019 ISPE Annual Meeting and Expo. Related topics include:
- Commissioning, Qualification and Validation of New Cell and Gene Facilities, presented by Wilbur G. Williams, Director Quality Engineering, Kite Pharma Inc., (Day 1, Innovation Forum);
- An Innovative Approach to Gene and Cell Therapy Facility Builds, presented in four lectures from Tony Khoury, VP, Project Farma, Christopher B. McDonald, VP Manufacturing, Kite Pharma Inc., Gregory R. Gara, VP Technical Operations & Engineering, AveXis Inc., and Brian L. Winstead, Sr. Program Manager, CSL Behring (Day 2, Innovation Forum)
- Enabling Productive and Flexible Facilities from the Nuts and Bolts to Bits and Bites, presented in three lectures from Chelsea S. Kuranda, CHEG, Lead Automation Engineer, GE Healthcare, Eric A. Ruldolph, VP, CSR, Single-Use, ABEC, and Scott T. Probst, PhD, Unit Head, PTD Biologics, Bayer–US LLC (Day 3, Innovation Forum).
Remember to also visit the 2019 ISPE Annual Meeting & Expo booths to gather additional information from a wide range of industry experts from architectural, engineering and construction (AE&C) firms, technology/equipment/facility design & fabrication companies and biopharmaceutical strategy and tactical service providers.
GET READY TO MODERNIZE. GLOBALIZE. TRANSFORM.
With 6 extensive education tracks, 85+ hours of targeted technical sessions, 24+ hours of networking opportunities, 200+ exhibitors, Discovery Stage in Expo Hall, 2 days of in-depth classroom training & more, the 2019 ISPE Annual Meeting & Expo is an event you don’t want to miss! Take advantage of the registration discount that is available through 17 September and register today.