Understanding Cleanliness Classifications for Life Science Facilities
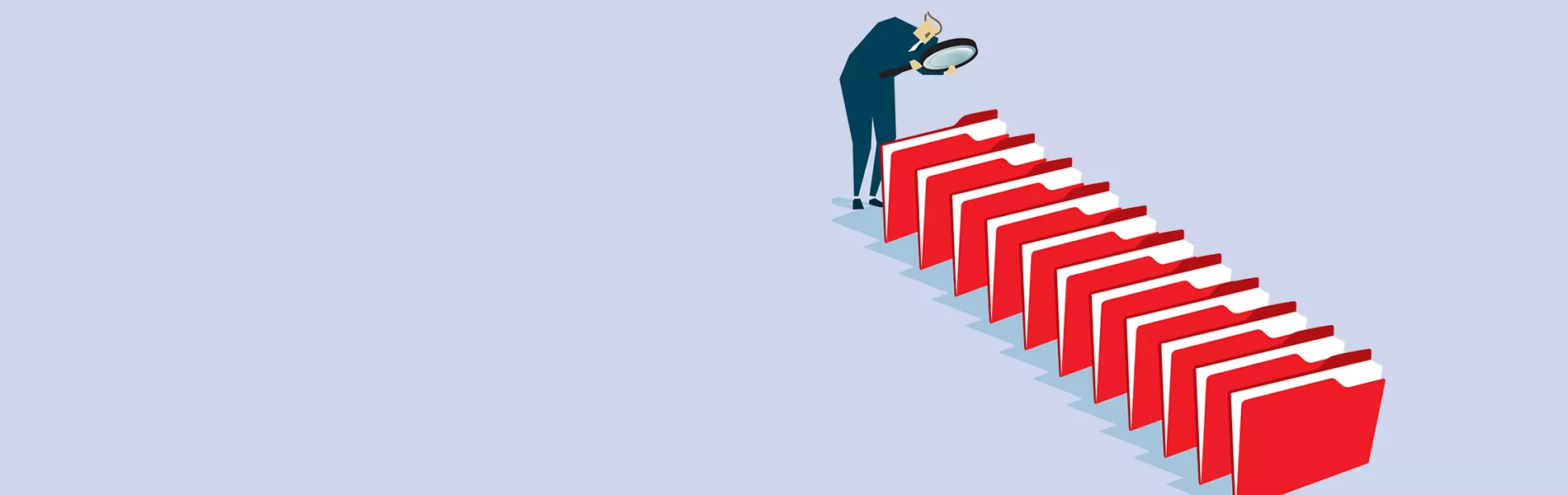
In recent years we have observed misunderstanding and confusion over correlation between the 2004 US Food and Drug Administration (FDA) environmental cleanliness requirements for sterile product manufacture 1 and those of the European Medicines Agency EudraLex Volume 4, Annex 1.2
This misunderstanding, which began before the demise of Federal Standard 209, has been exacerbated by the introduction of the ISO cleanliness classification system standards in 1999 (14644-1:1999) and most recently in the 2015 revisions (14644-1:2015). The situation has since become more critical because the Annex 1 requirements in are replicated virtually verbatim in the Pharmaceutical Inspection Co-operation Scheme (PIC/S) and World Health Organization (WHO) good manufacturing practice requirements, which are used by regulators around the world. Such broad adoption of virtually identical regulatory guidance based on the European Union (EU) system has also aggravated the situation.
The strong similarities between the systems are likely to have led to the common misapplication of designations and incorrect correlation between classification systems. In addition, subtle differences in the requirements can cause even greater confusion:
- Both EU and PIC/S require “in-operation” and “at-rest” classifications.
- Both EU and PIC/S specify a “cleanup” or “recovery” time and qualification thereof.
- The FDA standard classifies and monitors airborne particles at a single size threshold of ≥ 0.5 μm; EU and PIC/S use two size thresholds: ≥ 0.5 and 5.0 μm.
- EU and PIC/S airborne ≥ 5.0 μm particle concentration limits for grade A cleanliness do not align with ISO 5 class limits.
- Designation and qualification of a class below ISO 8 in operation (Grade C) as ISO 8 at rest (Grade D) vs. ISO 9 in operation or “controlled, not classified” (CNC).
Before beginning a discussion of differences within modern classification systems, it is perhaps advisable to review space classification before harmonization efforts led to the current systems.
ISPE has attempted to bridge these somewhat confusing differences with a single composite cleanliness grading system intended to satisfy international regulatory bodies and make good scientific sense.
FS 209
The classification of space by airborne particulate concentration began with Federal Standard 209 in 1963 and is the source for the classifications still used by the US Pharmacopeia and FDA (Table A): Other countries established standards that further complicated the terms and nomenclature affecting the design and cleanliness classification of global cleanroom facilities (Table B).
As you can see, our current issue of aligning two standards is small by comparison to the historical alignment of diverse global standards. What’s more, the current underlying harmonized standard for space classification serves to align regulations to a great degree. To fully understand the similarities and differences between regulatory requirements, we must understand the harmonized space classification system on which they are based.
Particle size, μm | |||||
---|---|---|---|---|---|
Class | 0.1 | 0.2 | 0.3 | 0.5 | 5.0 |
1 | 35 | 7.5 | 3 | 1 | - |
10 | 350 | 75 | 30 | 10 | - |
100 | - | 750 | 300 | 100 | - |
1,000 | - | - | - | 1,000 | 7 |
10,000 | - | - | - | 10,000 | 70 |
100,000 | - | - | - | 100,000 | 700 |
ISO 14644-1:1999 (superseded): This standard defined classes of cleanliness by airborne particle count concentration following a decimal system. The classes are illustrated in Table C for a series of size ranges. The relationship between ISO class number, particle number concentration, and reference particle size is defined in the standard by the formula Cn = 10N × (0.1 μm/D)2.08, where Cn is the particle count, N is the ISO class, and D is the particle mean diameter in μm.
ISO 14644-1:2015: This standard replaces ISO 14644-1:1999, but serves the same purpose as the prior standard (Table D), with some notable changes:
- There is no class limit particle count specified for ≥ 5 μm particles at ISO 5 due to the uncertainty of counting these large particles at low concentration.
- Monitoring ≥ 5 μm particles at low concentration must be done in concert with another particle size; the “macro particle” descriptor M should be added to communicate the uncertainty of the reading.
- The decimal classification system must be adjusted to 0.5 class increments (e.g. ISO 4, ISO 4.5, ISO 5)
Although this common standard now harmonizes space classifications in regulations across the world, differences in interpretation can result in some ambiguity.
Us FDA Application Of ISO Classifications
The 2004 FDA Guidance for Industry cited at the beginning of this article provides some clarification of the FDA use of ISO grades. At all grade levels the FDA assumes a particle size of ≥ 0.5 μm and that classification and monitoring occur with the room in operation. The guidance also assigns unique definitions to some classifications:
ISO 5: A space that has been classified to meet ISO 14644-1 requirements (3,520 particles/cubic meter) for airborne 0.5 μm particulate in the in-operation state. These spaces are constructed with a “flushing” or “sweeping” generally unidirectional airflow that protects critical areas, with a suggested velocity of 0.45 meters per second ±20%, or as justified and qualified via airflow visualization.
ISO 9: A space that has been classified to meet ISO 14644-1:1999 requirements (35,200,000 particles per cubic meter) for airborne 0.5 μm particulate in the in-operation state. This classification does not actually appear in FDA guidance but is found in some FDA-regulated facilities.
Terms and Definitions
Ambient environment: Environmental conditions where no HVAC systems are present.
Uncontrolled (UC): Areas where HVAC systems may be present, but no claim is made or qualified for the specific control of particulate, temperature, or humidity. These areas are sometimes referred to as “general” or “comfort-controlled” areas within pharmaceutical facilities such as office and technical space. May also be designated “not controlled (NC).”
Classified space: Areas in which HVAC systems are designed to reduce airborne contaminants below a specified level as defined in ISO 14644-1 (tested per ISO14644-2,3) and both temperature and RH are controlled more tightly than in the ambient environment. These areas must be performance verified/qualified. They may be tested to meet ISO requirements for airborne 0.5μm particulate and viable organisms in the “in-operation” state to meet US FDA requirements, or they may be tested to meet ISO requirements for airborne 0.5 and 5.0 μm particulate as well as viable organisms in both the “in-operation” state as well as the “at-rest” states to meet EMA and PIC/S requirements. Where EMA and PIC/S requirements are to be satisfied, the transition between the two states should take place in 15–20 minutes. This can be verified via the “recovery test” as specified in ISO 14644-3.
Recovery: A test defined in ISO 14644-3 that challenges room environmental performance by measuring the time required for contamination to reduce by 1 to 2 log after particle generation in the space ceases. ZLG Aide Memoire 07121104 Grade E: A classified space that satisfies the airborne viable microorganisms requirement of < 250 CFUs per cubic meter.
ZLG Aide Memoire 07121104 Grade E: A classified space that satisfies the airborne viable microorganisms requirement of < 250 CFUs per cubic meter.
ZLG Aide Memoire 07121104 Grade F: A classified space that satisfies the airborne viable microorganisms requirement of < 500 CFUs per cubic meter.
Particles per cubic meter ≥ 0.5 μm | US FS-209E, 1992 | US FS-209E equivalent per cubic foot | EU EudraLex Vol.4 Annex 1, 1997 | France AFNOR, 1989 | Germany VDI 2083, 1990 | Britain BS 5295, 1989 | Japan JISB 9920, 1989 | ISO 14644-1 and CEN 243 |
---|---|---|---|---|---|---|---|---|
1 | ||||||||
3.5 | 0 | 2 | 2 | |||||
10 | M1 | |||||||
35.3 | M1.5 | 1 | 1 | 3 | 3 | |||
100 | M2 | |||||||
353 | M2.5 | 10 | 2 | 4 | 4 | |||
1,000 | M3 | |||||||
3,530 | M3.5 | 100 | B: at rest A: at all times | 4,000 | 3 | E or F | 5 | 5 |
10,000 | M4 | |||||||
35,300 | M4.5 | 1,000 | 4 | G or H | 6 | 6 | ||
100,000 | M5 | |||||||
353,000 | M5.5 | 10,000 | 5 | J | 7 | 7 | ||
1,000,000 | M6 | |||||||
3,530,000 | M6.5 | 100,000 | 6 | K | 8 | 8 | ||
10,000,000 | M7 |
Particles per cubic meter (cubic foot), by size | ||||||
---|---|---|---|---|---|---|
ISO Class | 0.1 μm | 0.2 μm | 0.3 μm | 0.5 μm | 1 μm | 5 μm |
1 | 10 | 2 | 0 | 0 | 0 | 0 |
2 | 100 | 24 | 10 | 4 (0.1) | 0 | |
3 | 1,000 | 237 | 102 | 35 (1) | 8 | |
4 | 10,000 | 2,370 | 1,020 | 352 (10) | 83 | |
5 | 100,000 | 23,700 | 10,200 | 3,520 (100) | 832 | 29 |
6 | 1,000,000 | 237,000 | 102,000 | 35,200 (1,000) | 8,320 | 293 |
7 | 352,000 (10,000) | 83,200 | 2,930 | |||
8 | 3,520,000 (100,000) | 832,000 | 29,300 | |||
9 | 35,200,000 (1,000,000) | 8,320,000 | 293,000 | |||
1 cubic meter = 35.2 cubic feet When referring to US FDA guidance only the 0.5 μm particle size (highlighted) is measured © ISO. This material is reproduced from ISO 14644-1:1999 with permission of the American National Standards Institute (ANSI) on behalf of the International Organization for Standardization. All rights reserved. ISO 14644-1:1999 is an archived ISO document. It cannot be referred to as an approved ISO standard. |
Maximum allowable concentrations Particles per cubic meter for particles equal to and greater than the sizes shown [a] | ||||||
---|---|---|---|---|---|---|
ISO Class | 0.1 μm | 0.2 μm | 0.3 μm | 0.5 μm | 1 μm | 5 μm |
1 | 10[b] | [d] | [d] | [d] | [d] | [e] |
2 | 100 | 24[b] | 10[b] | [d] | [d] | [e] |
3 | 1,000 | 237 | 102 | 35 [b] | [d] | [e] |
4 | 10,000 | 2,370 | 1,020 | 352 | 83[b] | [e] |
5 | 100,000 | 23,700 | 10,200 | 3,520 (100) | 832 | [d–f] |
6 | 1,000,000 | 237,000 | 102,000 | 35,200 (1,000) | 8,320 | 293 |
7 | [c] | [c] | [c] | 352,000 (10,000) | 83,200 | 2,930 |
8 | [c] | [c] | [c] | 3,520,000 (100,000) | 832,000 | 29,300 |
9 | [c] | [c] | [c] | 35,200,000 (1,000,000) | 8,320,000 | 293,000 |
© ISO. This material is reproduced from ISO 14644-1:2015 with permission of the American National Standards Institute (ANSI) on behalf of the International Organization for Standardization. All rights reserved. |
EU, PIC/S, and WHO
EudraLex Volume 4, Annex 1 requirements for sterile products stipulate in-operation and at-rest airborne particle count limits at both ≥ 0.5 and 5.0 μm particle sizes. It further directs that spaces recover from the in-operation to the at-rest state after a 15–20-minute cleanup period. Some other unique definitions are:
Grade A: A classified space that satisfies European Medicines Agency (EMA) and PIC/S requirements to meet:
- ISO 5 measured via airborne ≥ 0.5 μm particulate
- ISO 4.8* measured via airborne ≥5.0 μm particulate in the in-operation and at-rest states
- Airborne viable microorganisms < 1 colony forming unit (CFU) per cubic meter
These spaces are normally unidirectional flow with a suggested air velocity of 0.36–0.54 meters per second. These spaces surround product only and must be absent of people.
Grade D: A classified space that satisfies EMA and PIC/S requirements to meet ISO 8 measured via:
- Airborne 0.5 and 5.0 μm particulate in the at-rest state only
- Airborne viable microorganisms < 200 CFUs per cubic meter.
Aside from these differences in particle size and operational state, there is a good deal of alignment between the classification systems for the US, EU, PIC/S, and WHO. We summarize these similarities and differences in Table E.
The table’s colored areas show areas of alignment between regulations, while the yellow areas show the differences between the US and other classification systems. Although US, EU, PIC/S, and WHO systems have four identified classes, they do not map directly, as each has one class the others do not.
ISPE has attempted to bridge these somewhat confusing differences with a single composite cleanliness grading system intended to satisfy international regulatory bodies and make good scientific sense.
To meet these objectives, the ISPE HVAC Community of Practice suggested that the ISPE grading system, originally proposed in the second edition of Sterile Products Manufacturing Baseline™ Guide, be modified as shown in the 2013 Baseline Guide Volume 6: Biopharmaceutical Facilities (Table F and Table G).
* The use of ISO 4.8 in lieu of ISO 5 for 5.0 μm particles in Grade A appears to be the result of aligning this limit on the lowest number possible, working ISO 14644 sample size calculations backward using a 1 cubic meter sample size.
This unified system can help eliminate common misunderstandings about classification alignment and clarify the intent of environmental control within facilities.
Revised ISPE Grades
The ISPE Sterile Guide team has suggested a further refinement, replacing the ISPE grades with a US/EU designation as follows:
Grade 8 (ISO 8/Grade C): A classified space that satisfies FDA requirements for:
- ISO 8 measured via airborne 0.5 μm particulate in the in-operation state
- EMA and PIC/S requirements to meet ISO 8 measured via airborne 0.5 and 5.0 μm particulate in the in-operation state
- ISO 7 measured via airborne 0.5 and 5.0 μm particulate in the at-rest state, with a 15–20-minute transition between states
- Airborne viable microorganisms < 100 CFUs per cubic meter
Grade 7 (ISO 7/Grade B): A classified space that satisfies FDA requirements for:
- ISO 7 measured via airborne 0.5 μm particulate in the in-operation state
- EMA and PIC/S requirements to meet ISO 7 measured via airborne 0.5 and 5.0 μm particulate in the in-operation state
- ISO 5 measured via airborne 0.5 and 5.0 μm particulate in the at-rest state, with a 15–20-minute transition between states
- Airborne viable microorganisms < 10 CFUs per cubic meter
Grade 5 (ISO 5/Grade A): A classified space that satisfies FDA requirements for:
- ISO 5 measured via airborne 0.5 μm particulate in the in-operation state
- EMA and PIC/S requirements to meet ISO 5 measured via airborne 0.5 μm particulate
- ISO 4.8 measured via airborne 5.0 μm particulate in the in-operation and at-rest states
- Airborne viable microorganisms < 1 CFU per cubic meter. These spaces are normally unidirectional flow with an air velocity of 0.20–0.45 meters per second.
Controlled not classified with local monitoring (CNC+/Grade D): Areas where HVAC systems are designed to reduce airborne contaminants below the level of the ambient environment and in which both temperature and relative humidity (RH) are controlled more tightly than in the ambient environment. Claims for environmental control in these areas are related to both system design and system performance; installation qualification and operational qualification are common.
These areas are typically qualified to meet ISO 8 requirements at rest only, and to control temperature and humidity within a specified band. They are monitored for viable particulate during operation to provide background information for investigations and to assure adequate layers of closure. These areas are generally aligned with PIC/S designation Grade D and airborne viable microorganisms < 200 CFUs per cubic meter.
Controlled not classified (CNC): Areas where HVAC systems are specifically designed to reduce airborne contaminants below the level of the ambient environment and both temperature and RH are controlled more tightly than in the ambient environment. Claims for environmental control in these areas are related to the design of the system; installation qualification is common. No claim is made or qualified for the specific control of particulate. Typical systems will have heating, cooling, and filtration meeting minimum efficiency reporting values of 13 or better. These areas are sometimes referred to as “pharmaceutical” or “clean” areas within pharmaceutical facilities.
Temperature controlled: Areas where HVAC systems are specifically designed to control both temperature and (where applicable) RH more tightly than in the ambient environment. Temperature and RH are usually qualified in these areas and temperature mapping is expected. This is designation is typically found in warehouse spaces, cold rooms, and logistics. Some companies apply the CNC designation for these areas.
This unified system of classification, whether by stating the grade and ISO number or by referencing both the ISO class and the EU grade can help eliminate common misunderstandings about classification alignment and clarify the intent of environmental control within facilities.
In closing, the authors offer terms and definitions to clarify any remaining confusion regarding common classification and environmental control terminology.
FDA | In-operation (particles per cubic meter) | Active air action | EU, WHO, PIC/S | In-operation (particles per cubic meter) | At-rest (particles per cubic meter) | Active air action | |||
---|---|---|---|---|---|---|---|---|---|
ISO | USP | 0.5 μm | Limits | Grade | 0.5 μm | 5.0 μm | 0.5 μm | 5.0 μm | Limits |
ISO 5 | 100 | 3,520 | 1 | A | 3,520 | 20 | 3,520 | 20 | < 1 |
ISO 6 | 1,000 | 35,200 | 7 | N/A | |||||
ISO 7 | 10,000 | 352,000 | 10 | B | 352,000 | 2,900 | 3,520 | 29 | 10 |
ISO 8 | 100,000 | 3,520,000 | 100 | C | 3,520,000 | 29,000 | 352,000 | 2,900 | 100 |
N/A | N/A | N/A | N/A | D | N/A | N/A | 3,520,000 | 29,000 | 200 |
ISO Class | USP particles per cubic foot | US FDA in-operation limit, particles per cubic meter | EU and PIC/S grade | EU and PIC/S | ZLG “aide-memoire” 07121104 | Active air action limits, colony-forming units per cubic meter | ||||
---|---|---|---|---|---|---|---|---|---|---|
In-operation limit, particles per cubic meter | At rest limit, particles per cubic meter | |||||||||
≥ 0.5 μm | ≥ 0.5 μm | ≥ 0.5 μm | ≥ 5.0 μm | ≥ 0.5 μm | ≥ 5.0 μm | |||||
ISO 5 | 100 | 3,520 | A | 3,520 | 20 | 3,520 | 20 | N/D | < 1 | |
ISO 6 | 1,000 | 35,200 | N/D | 35,200 | 290 | 3,520 | 29 | N/D | 7 | |
ISO 7 | 10,000 | 352,000 | B | 352,000 | 2,900 | 3,520 | 29 | N/D | 10 | |
ISO 8 | 100,000 | 3,520,000 | C | 3,520,000 | 29,000 | 352,000 | 2,900 | N/D | 100 | |
ISO 9 | 1,000,000 | 35,200,000 | N/D | N/A | N/A | N/A | N/A | N/D | N/D | |
N/A | N/A | N/A | D | N/A | N/A | 3,520,000 | 29,000 | N/D | 200 | |
N/D | N/A | N/A | N/D | N/A | N/A | N/A | N/A | E | 250 | |
N/D | N/A | N/A | N/D | N/A | N/A | N/A | N/A | F | 500 | |
CNC* | N/A | N/A | N/D | N/A | N/A | N/A | N/A | N/D | N/A | |
U/C* | N/A | N/A | N/A | N/A | N/A | N/A | N/A | N/D | N/A | |
* Not ISO classes; these are common designations without a standard definition |
ISPE grade | In-operation limit, particles per cubic meter | At-rest limit, particles per cubic meter | Active air action limits, colony-forming units per cubic meter | ||
---|---|---|---|---|---|
≥0.5 µm | ≥ 5.0 µm | ≥ 0.5 µm | ≥5.0 µm | ||
Grade 5 | 3,520 | 20 | 3,520 | 20 | <1 |
Grade 6 | 35,200 | 290 | 3,520 | 29 | 7 |
Grade 7 | 352,000 | 2,900 | 3,520 | 29 | 10 |
Grade 8 | 3,520,000 | 29,000 | 352,000 | 2,900 | 100 |
CNC+* | N/A | N/A | 3,520,000 | 29,000 | 200 |
CNC* | N/A | N/A | N/A | N/A | N/A |
UC* | N/A | N/A | N/A | N/A | N/A |
† 2013 Biopharmaceutical Facilities Baseline Guide * Not ISO classes; these are common designations without a standard definition |
Notes on Tables F and G
- N/D = not designated
- Values may be averages; EU and PIC/S require measurement of particles up to and including 0.5 μm and 5 μm, the US standard requires 0.5 μm, hence the table incorporates both to ensure compliance with the most stringent requirement.
- Samples from Grade 5 areas should normally show no viable organisms.
- Recovery from the in-operation to the at-rest state should be verified to occur within 15–20 minutes for ISPE grades 6, 7, and 8. The recovery test as defined in ISO 14644-3:2005 and IEST RP003 may be carried out to verify a one or two log reduction test. Recovery testing may also be performed for informational purposes.
- At-rest figures are given to support recovery and “static” room classification testing. Maintenance of these levels during idle (not in use) periods is not intended
.
Editor's Note: The online version of this article has been updated to correct a typographical error in the Table E header in the print version.
- 1US Food and Drug Administration. Guidance for Industry. “Sterile Drug Products Produced by Aseptic Processing—Current Good Manufacturing Practice.” September 2004. <a href="http://www.fda.gov/downloads/drugs/guidancecomplianceregulatoryinformation/guidances/ucm07032.pdf">http://www.fda.gov/downloads/drugs/guidancecomplianceregulatoryinformation/guidances/ucm07032.pdf</a>
- 2European Commission. EurdraLex. Volume 4, Annex 1. “Manufacture of Sterile Medicinal Products (corrected version).” <a href="http://ec.europa.eu/health//sites/health/files/files/eudralex/vol-4/2008_11_25_gmp-an1_en.pdf">http://ec.europa.eu/health//sites/health/files/files/eudralex/vol-4/2008_11_25_gmp-an1_en.pdf</a>