Shifts in Container Closure Integrity Test Methods
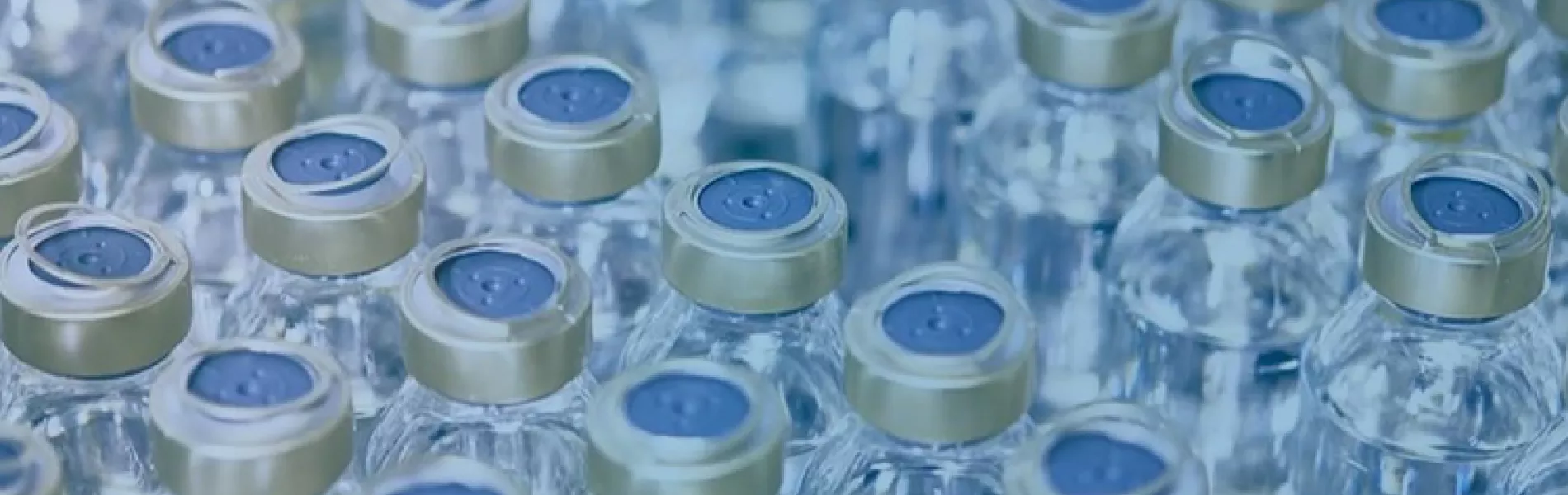
Newer container closure integrity (CCI) test methods are more accurate and reliable than longtime industry standards. Transitioning to include deterministic testing alongside probabilistic methods may seem daunting at first, but it is in the industry’s best interest.
Container closure integrity is determined by evaluating whether a given container maintains its sterile barrier. With the August 2016 revision of United States Pharmacopeia (USP) Chapter <1207>, “Package Integrity Evaluation—Sterile Products,” the industry has begun to shift from probabilistic to deterministic container closure integrity testing methods. Probabilistic methods generally require a series of stochastic, sequential events that are outside the operator’s control. Deterministic test methods follow a predictable chain of events and use controlled test equipment to capture an objective measurement of leakage.1 USP Chapter <1207> guides industry professionals on container closure integrity testing, including available methods and which considerations are appropriate to evaluate when deploying a test method. The tests used to determine container closure integrity have critical effects on product stability and patient safety, so it is vital to use the best method for a particular container in the interests of saving time and money and ensuring patient health.1
When evaluating different leak-testing methods, it is important to understand that all packages leak to a certain degree. Maximum allowable leakage limits (MALL) are set for each package type and product configuration to provide a basic target for ensuring container closure integrity. For parenteral product classes, defects in the single-micrometer range are considered critical.2
Probabilistic Methods and Deterministic Alternatives
Historically, probabilistic container closure integrity test methods such as water bath, dye, and microbial ingress tests have been used to determine package quality. These tests are limited in their effectiveness and reliability for several reasons. Chief among them are the subjectivity of the results, the lack of standardization, and the lack of control a test operator has over certain stochastic elements of the test process. Also, these test methods lack industry standardization, with different sites using different chemistries, cycle times, and test parameters to achieve test results.
Most container closure integrity test methods apply a condition to the test sample to then observe a response. In an ideal test method, little sample preparation would be required and method deviation would be reduced by limiting the steps involving operator intervention. The test conditions applied to the test sample should be measured and controlled. The final test method observation should not be subjective or variable; rather, it should be a measurement that can be traced back to certified, calibrated standards. Deterministic methods eliminate variability where possible and improve clarity with regard to the samples being tested.
Deterministic leak testing, such as vacuum decay, high-voltage leak detection (HVLD), or headspace analysis,3 ,4 is based on phenomena that follow a predictable chain of events. Leakage is measured using physicochemical technologies that are readily controlled and monitored, yielding objective quantitative data.1 Deterministic leak tests are performed on calibrated machines designed to control potential variables, perform uniformly under varying conditions, produce traceable test results quickly, and detect smaller leak sizes with greater reliability than probabilistic methods.
The critical nature of container closure integrity tests and the implications they have for patient safety make accuracy of the test result paramount. While a probabilistic test may still be effective for certain applications, shifting to methods with greater reliability clearly has distinct value. Table 1 lists the factors that must be considered and provides questions to help determine which testing methodology to use based on common package/product combinations.
Question | Oral Dose Tablet in Aluminum Cold Form (e.g., Thyroid Hormone) |
Parenteral (Biologic Liquid-Filled Vial) |
---|---|---|
What characteristics are important to patient safety? How does the product achieve this? | Prevents oxidation of the product by maintaining barrier properties and package integrity. | Chemical stability of the product; product sterility (no microbial growth). Leaks in the single-digit-micron range pose risks; must ensure that the sterile barrier is maintained. |
To what level should that package characteristic be challenged, commensurate with the level of acceptable risk associated with patient safety? | Oxidation level is contingent on the blister package’s headspace and defect size (Fick’s first law). | Down to the single-digit-micrometer range, in accordance with as many samples as can be reliably tested. Test an appropriate quantity down to the critical defect size to achieve statistically relevant assessment of the batch. |
Critical Follow-up Questions | ||
|
Alternatives to the Bubble Emission Leak Test
The bubble emission leak test is described in USP Chapter <1207> as a probabilistic test to detect gas leaks in containers. The method involves submerging a container in water and applying a vacuum. Any bubbles streaming from the container indicate a leak. A variety of factors contribute to the probabilistic characterization of the bubble emission method.1 ,5
- The size of leak that can be detected depends on the water surface tension and the pressure differential between the water bath and the inside of the container.
- A stream of bubbles will only be generated when there is a pressure differential between the inside of the container and the outside.
- A flexible package will expand under the vacuum, reducing the pressure differential, which is needed to create a stream of bubbles.
- Pouches with varying shapes and volumes will achieve different differential pressures and will be more or less able to generate a stream of bubbles from the same size leak.
- Liquid may interact with hydrophilic container contents to plug a leak.
- The negative test pressure may be a gauge or absolute pressure level, which will have implications when performing the same test at different elevations.
An alternative to the bubble emission leak test would be a vacuum decay leak test that is deterministic. Ideal vacuum decay systems will draw an absolute vacuum (not gauge) on the container in a controlled test space and monitor the vacuum level for any fluctuation. For flexible packaging, a flexible membrane would be beneficial, compensating for shape and volume variations between samples. The vacuum decay measurements include the final pressure and the change in pressure in the test chamber during the test cycle, producing an accurate and traceable measurement of leakage for each test cycle. The vacuum decay test method outweighs the water bath in sensitivity, reliability, and overall test method reproducibility.1 ,5
Alternatives to Dye Ingress
The dye ingress method is similar to the water bath but requires a series of events to occur for a defect to be effectively detected. The method begins with submerging the container beneath a dye solution inside a vacuum vessel and drawing vacuum on the vessel. Next, in stage 2 of the test, a defective sample under the vacuum would need to leak contents into the dye solution. In stage 3, the vessel is brought back to atmospheric pressure, and the vacuum that had been developed inside the container in stage 2 would draw dye back into the container. The primary probabilistic challenges facing dye ingress are associated with stage 2 of the test cycle:4
- Enough volume needs to be evacuated from the container during stage 2 of the cycle to create sufficient vacuum inside the container to draw the dye into the container.
- If there is little to no air inside the container, little to no force will be generated in stage 2 to draw liquid from the container. In this circumstance, dye ingress in stage 3 is highly probabilistic.
- If there is air in the container, the chemical properties of the container contents will determine how effectively fluid contents can leak out of the container during stage 2. The vacuum applied in stage 2 will be less effective at drawing liquid from the container, especially with more viscous liquids.
The US Food and Drug Administration and the European Commission’s Annex 1 require container closure integrity testing to be performed with actual product or product mimicking the natural product physical and chemical conditions. Generally, there is little standardization for the dye ingress test, and the impact of container conditions on the method’s performance further impedes the method’s capability.4
Two alternatives to the dye ingress method are vacuum decay and high-voltage leak detection. The methods are vastly different in approach. Vacuum decay was described in the discussion of the bubble emission leak test as a deterministic test method. Under certain circumstances, specifically in testing proteinaceous aqueous solutions, vacuum decay may be less effective. With a vacuum-based test, proteinaceous or viscous contents can dry up within a container leak, sealing it off.4
When testing a proteinaceous or viscous liquid, the better alternative would be to test using high-voltage leak detection, which uses the principles of electrical capacitance to detect leaks in pharmaceutical containers. The technology can be calibrated and produces reliable and repeatable detection of defects under a wide range of product chemistries and container presentations. Method input factors are highly controlled and traceable to electrical standards.
Embracing the Shift
Notably, each of the probabilistic test methods described in this article is a destructive test—the sample is adulterated upon completion. With less-expensive products, this may not be a particularly pressing concern. However, the ability to repeat an experiment is a cornerstone of good science, and container closure integrity testing is increasingly becoming a science-based discipline. Destructive testing results are finite, and samples cannot be used for further analysis, regardless of the results.
Most deterministic methods are considered to be nondestructive, which means the tests can be repeated without damaging the sample in the process. Therefore, the test sample can be released into the supply chain after its integrity is confirmed. In instances where a nondestructive method shows that the sample’s container closure integrity is compromised, the unadulterated sample can be inspected and analyzed further.
Shifting to a deterministic method for products in development requires that the physiochemical aspects of a product be evaluated to determine which test method is most appropriate. A third-party GMP lab can perform a full-scale test method development on the target product and provide significant guidance regarding the appropriate path forward. The test method developed by a GMP lab can be transferred directly to the manufacturing site.
Many in the industry are reluctant to embrace the shift from traditional probabilistic testing toward newer deterministic methods, and this is understandable. Transferring away from a probabilistic method for a product in production is often avoided because it involves significant effort for refiling. However, in the corrective-action period following a quality deviation, the rationale for shifting test methodology to a deterministic method becomes clearer.
The upfront costs of new test equipment is often a deterrent. But manufacturers should also consider how much value can be generated by deploying a reliable deterministic test method, as well as the costs that add up when using less-reliable probabilistic methods. If inaccurate information is impacting a successful batch release or obscuring stability data, there is a significant and real cost to that.
Deterministic test methods can provide quantitative results in a matter of seconds. Such quick results translate to quicker preventive actions, if necessary, without needing to discard large batches of product—saving time, money, and resources. Over a short period of time, deterministic technologies and the information they produce should provide significant returns on the investment.
Others may believe the traditional methods work adequately. However, having an acceptable status quo ought not be a reason to avoid updating best practices; the more options the industry has, the better container closure integrity test methods can be tailored for each package/product combination. There is no single method that works for all package and product combinations, but sites operating with general product classes will often find a single suitable test method for that specific product class.
Deploying New Test Methods
USP Chapter <1207> explains the importance of investigating the interaction between the package and the product when selecting a test method. Because the physics behind container closure integrity tests are the foundation for the method’s effectiveness, two criteria are paramount: vetting the physiochemical properties of the application and outlining the direct, practical nature of what the method measures.
Addressing the physicochemical nature of a container closure integrity application requires asking many questions about the package and product combination. The product will often determine what sensitivity is required and which test method is optimal. What is the maximum allowable leakage limits, for example? If the product is parenteral, a risk assessment would show the need to challenge container closure integrity to a high level of sensitivity to prevent microbial contamination. On the other hand, a radioisotope may be not affected by microbial ingress, but it may have a greater risk of product degradation from chemical contaminants. A lower-risk oral dose ap-plication may be relatively insensitive to environmental contaminants, but other, more sensitive ingredients may oxidize easily.
Conclusion
While some traditional methods have practical application in evaluating package quality, there is a clear case for evolving container closure integrity determination to deterministic methods. For applications in which the test results have a high-stakes impact, there are aspects to each probabilistic method that preclude them from being considered over deterministic methods.
- 1 a b c d e United States Pharmacopeia. USP Regulatory Guidance Document: Chapter <1207> Package Integrity Evaluation—Sterile Products.
- 2Kirsch, L. E., L. Nguyen, C. S. Moeckly, and R. Gerth. “Pharmaceutical Container/Closure Integrity. II: The Relationship Between Microbial Ingress and Helium Leak Rates in Rubber-Stoppered Glass Vials.” PDA Journal of Pharmaceutical Science and Technology 51, no. 5 (September–October 1997): 195–202.
- 3Victor, K., L. Levac, M. Timmins, and J. Veale. “Method Development for Container Closure Integrity Evaluation via Headspace Gas Ingress by Using Fre-quency Modulation Spectroscopy.” Journal of Pharmaceutical Science and Technology 71, no. 6 (November–December 2017): 429–53. doi: 10.5731/pdajpst.2017.007518.
- 4 a b c d Wolf, H., T., Stauffer, S. Y. Chen, Y. Lee, R. Forster, M. Ludzinski, M. Kamat, B. Mulhall, and D. M. Guazzo. “Vacuum Decay Container/Closure Integrity Testing Technology. Part 2. Comparison to Dye Ingress Tests.” Journal of Pharmaceutical Science and Technology 63, no. 5 (September–October 2009): 489–98.
- 5 a b American Society for Nondestructive Testing. Leak Testing. Vol. 1 of Nondestructive Testing Handbook, 3rd ed. Columbus, OH: American Society for Non-destructive Testing, 1998.